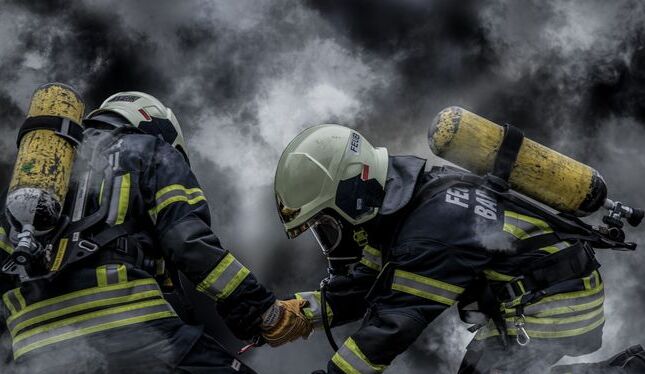
OSHA 1926.65(l): Emergency Response at Uncontrolled Hazardous Sites
-
Written Emergency Plan
- Employers involved in uncontrolled site clean-ups or corrections must prepare a written emergency response plan before starting work, according to OSHA1926.65: Emergency Response.
- This plan should be accessible to employees, their representatives, OSHA inspectors, and relevant agencies.
- Employers who plan a complete evacuation and allow no staff intervention can follow the simpler emergency action plan per § 1926.35 instead.
-
Required Elements of Emergency Response Plan
Your site Emergency Response Plan must address according to OSHA1926.65: Emergency Response which are listed below
- Pre-emergency planning
- Roles, communication, and authority lines
- Hazard recognition and prevention
- Safe distances and refuge zones
- Site security and access control
- Evacuation routes and procedures
- Decontamination steps (if not detailed elsewhere)
- Emergency medical treatment/first aid
- Alert systems and response steps
- Post-incident review and follow-up actions
- Necessary PPE and emergency gear
-
Integration & Updates
- The plan must align with local, state, and federal emergency response frameworks, including those from fire departments and other agencies.
- It should be regularly practiced through drills and updated as site conditions change.
Emergency Response Procedures (1926.65(l)(3))
When developing your Emergency Response Plan, according to OSHA1926.65: Emergency Response which are listed below
- Site design & weather:
- Incident reporting: Establish clear steps for notifying local, state, and federal agencies when needed
- Separate ERP section: Emergency procedures should be a clearly marked section within the Site Safety & Health Plan
- Plan compatibility: Ensure your plan integrates with local/state emergency response systems
- Practice drills: Conduct regular rehearsals to ensure teams know how to respond
- Frequent reviews: Update the plan as site conditions evolve or after actual emergencies
- Alarm systems: Install clear, loud alarms to halt operations and signal emergencies
- On-the-spot evaluation: During an incident, assess conditions quickly and activate the appropriate response steps
Lighting Requirements 1926.65(m)
- Worksite lighting: Any area accessible to employees must have minimum illumination levels as specified in OSHA’s Table D‑65.1 whenever work is underway.
TABLE D-65.1 – MINIMUM ILLUMINATION LEVEL IN FOOT-CANDLES | |
Foot-candles | Area or operations |
5 | General site zone. |
3 | Excavated/waste/access way/storage areas/loading/refueling/maintenance areas. |
5 | Indoors, Warehouses/corridors/hall/exit area. |
5 | Tunnels, shafts, and general underground work areas. (Exception, Minimum of 10 foot-candles, when drilling mucking/scaling.
In Mining, cap light, acceptable in the tunnel heading.) |
10 | General shops (e.g., mechanical/electrical equipment area, storerooms, barracks or living area, locker/dressing area, dining room, and indoor toilet/workroom.) |
30 | First aid stations, infirmaries, and offices. |
Clean Water & Supplies (1926.65 n(1)–(2))
- Drinking water: Provide enough clean water in sealed, tap-equipped containers—no scooping allowed. Clearly label water systems and don’t use for other purposes. Include disposable cups and disposal bins.
- Non-potable water (e.g., for firefighting): Must be clearly marked—and never cross-connected with drinking water supplies.
Restroom Facilities (1926.65 n(3))
- Provide toilets based on staff count:
- ≤ 20 workers: 1 toilet
- 21–200: 1 toilet + 1 urinal per 40 workers
- 200: 1 toilet + 1 urinal per 50 workers
- At least 1 toilet, for all temporary sites.
- Where no sewer exists, use chemical, recirculating, combustion toilets, or privies—unless local rules forbid.
- Toilet doors must have interior locks.
Washing, Showers & Changing Areas (1926.65 n(6)–(7))
- Provide hand-washing stations near the work area, with soap, running water (hot or warm), and individual towels or air dryers.
- For work exceeding six months where exposure exists:
- Showers must meet OSHA’s hot/cold water and towel standards
- Changing room must separate and clean
Other Facilities (n(4)–(5))
- Food areas: Must comply with local health rules and follow hygienic practices.
- Sleeping quarters (if provided): Must be properly heated, ventilated, and lighted.
TABLE D-65.2 – TOILET FACILITIES | |
Number of employees | Minimum number of facilities |
20 or fewer | One. |
More than 20, fewer than 200 | 1 toilet seat, 1 urinal per 40 |
More than 200 | 1 toilet seat, 1 urinal per 50 |
Sanitation at Short-term Hazardous Waste Sites 1926.65 n3.5
Essential Toilet Access
- At least 1 toilet, available in all conditions.
- Where no sewer exists, choose one of:
- Chemical toilet
- Recirculating toilet
- Combustion toilet
- Flush toilet
(Unless prohibited by local rules.)
- Mobile crews with nearby facility access are exempt.
- Toilet doors must have interior locks for privacy.
Food & Sleeping Areas
- Food services comply with local public health standard.
- Temporary sleeping area ventilated and lit.
Hygiene Facilities
- Hand-washing stations are required close to work areas where hazards could contaminate workers—ensure soap, water, and towels are available.
- If cleanup lasts six months or more, showers and change rooms are mandatory. located in clean air/provide ventilation.
1926.65(p): TSD Facility Safety & Health Requirements
- Written Safety & Health Program (p.1)
Employers at Treatment, Storage, and Disposal (TSD) facilities must maintain a written safety and health program. This document must outline hazard identification, control methods, emergency response (per p.8), jobsite analysis, engineering controls, exposure limits, waste-handling procedures, and technological updates—and be accessible to employees and OSHA.
- Hazard Communication (p.2)
A hazard communication program must be included per OSHA’s Hazard Communication Standard (1926.59).
- Medical Surveillance (p.3)
Employers must follow the medical surveillance requirements outlined in section (f).
- Decontamination (p.4)
Implemented in compliance, section (k).
- New Technology (p.5)
Employers should develop procedures to evaluate and adopt new safety technologies (per section (o)).
- Material Handling (p.6)
Procedures must address the safe handling of drums and containers, in line with section (j).
- Training Program (p.7)
- New workers at TSD sites need 24 hours of initial training, plus 8‑hour annual refreshers. They also receive a certificate upon completion.
- Current workers can substitute prior relevant training or experience, but must still take 8‑hour yearly refreshers.
- Trainers must be qualified—either they must have completed “train-the-trainer” courses or have the educational and practical background required.
- Emergency Response Plan (p.8)
Employers must integrate an Emergency Response Plan (ERP) into their written program. This plan should align with any required EPA contingency plans and include all typical ERP elements—unless the company simply chooses to evacuate staff, in which case they can follow the simpler emergency action plan (1926.35) instead.
Emergency Response Training Requirements (1926.65(p)(8)(iii))
- Essential Training for Responders
- Employees must be trained before participating in actual emergency responses.
- Training must include:
- Emergency Response Plan overview
- Site-specific Standard Operating Procedures (SOPs)
- Proper use of PPEs
- Emergency handling procedures
Two exceptions allow limited training:
- Exception 1: Only those designated for emergency control need full training; others just require awareness training to identify emergencies and alert fully trained responders.
- Exception 2: If an external fully trained response team is pre-arranged, only awareness-level training is needed for on-site employees to recognize emergencies and summon help.
- TSD Facility Response Teams
- Team must be trained according to OSHA1926.65: Emergency Response which are listed below
- Identify health and safety risks
- Use control equipment safely
- Select and wear correct PPE
- Communicate effectively and coordinate actions
- Respond to overexposure incidents and recognize related symptoms
- Certification & Competency
- Employers must document that each responder has completed required training or demonstrated equivalent competency.
- This certification must be re-validated annually, with records maintained by the employer.
Emergency Response Plan Enhancements (1926.65(p)(8)(iv))
In addition to standard ERP elements, you must include:
- Site layout & weather conditions
- Regulatory reporting procedures
- Plan alignment with local/state emergency systems
- Regular drills in training drills
- Periodic plan reviews and updates
- Overhead alarms to signal emergencies
- On-call decision-making to activate response actions promptly
Emergency Response to Hazardous Substance Releases (1926.65(q))
Plan & Purpose (q.1–2)
- Employers must create a written Emergency Response Plan (ERP) before starting emergency response duties, covering site, hazards, and response steps. The plan must be accessible to employees and OSHA
- Employers who simply evacuate and do not conduct response actions can provide a simpler Emergency Action Plan under § 1926.35
ERP must include according to OSHA1926.65: Emergency Response which are listed below:
- Pre-emergency plan/coordination with other responders
- Roles, communication, and training requirements
- Hazard recognition and prevention strategies
- Safe distances, refuge zones, and site control
- Evacuation routes, decontamination, medical first aid
- Alarm systems, PPE, and follow-up/critique procedures
- Integration with local/state plans
Incident Command System & Response Actions (q.3)
- The first senior responder on scene activates the Incident Command System, coordinating all response personnel and communications
- The ICS leader must:
- Identify hazards and implement engineering controls
- Ensure the correct PPE is used
- Require positive-pressure breathing apparatus for inhalation hazards until safe levels are confirmed by monitoring
- Limit site access using a buddy system in high-risk zones
- Position backup teams and first-aid responders on standby
- Appoint a safety officer to halt unsafe conditions and coordinate corrections
- Oversee decontamination, post-response
- Compressed-air cylinders for SCBA must meet DOT and NIOSH standards and be interchangeable as needed.
Support Personnel & Training (q.4–6)
- Temporary support workers (e.g., equipment operators) don’t need full emergency training but must receive a site-specific briefing covering PPE, hazards, and duties
- Specialized staff called in for technical advice must undergo annual competency-based training.
- All responders need training appropriate to their roles—ranging from basic awareness to advanced incident commander—before engaging in actual incidents .
Continuous Training & Medical Oversight (q.8–9)
- Annual refresher training or equivalent competency demonstration is mandatory to maintain readiness
- Responders showing exposure symptoms during or after an incident must receive prompt medical consultation as outlined in § (f)(3)(ii)
Emergency Response Training & Support (1926.65(q)(4)–(6))
- Skilled Support Personnel (q)(4)
- Temporary equipment operators (e.g., crane or digger operators) called to emergency sites are exempt from full responder training—even if exposed to hazards.
- They must receive a site-specific safety briefing that covers required PPE, chemical dangers, and their assigned tasks.
- Specialist Employees (q)(5)
- Demonstrate annual competency in their specialty.
- Responder Training Levels (q)(6)
Training varies by role and must be completed before any live emergency participation:
- Awareness Level (Find & report):
Basic understanding of hazards, recognition, and notification procedures. No action beyond alerting authorities. - Operations Level (Defensive response):
Minimum 8 hours of training, covering hazard assessment, PPE use, containment tactics, and decontamination techniques. - Hazmat Technician (Hands-on release control):
Minimum 24 hours training beyond operations level. Includes in-depth response plan implementation, equipment use, hazard classification, ICS roles, and decontamination. - Hazmat Specialist (Technical experts & liaisons):
Also 24+ hours, focused on advanced hazard analysis, liaison duties, state/local plans, and strategic planning. - On‑Scene Incident Commander:
At least 24 hours, plus leadership on implementing response systems, managing chemical PPE risks, and coordinating multi-agency actions.
- Certification, Refreshers & Trainers
- Employers must certify training and ensure annual refreshers or demonstrated competency for all roles.
- Trainers must be qualified through accredited courses or relevant teaching credentials.
On‑Scene Incident Commander Training (q)(6)(v)
- 24+ hours of training
- Must understand and apply according to OSHA1926.65: Emergency Response which are listed below
- The company’s Incident Command System (ICS) and Emergency Response Plan
- Chemical protective gear, including limitations and hazards
- Key local, state, and federal response plans
- Proper decontamination techniques
Trainers (q)(7)
- Instructor credentials must align with recognized standards (e.g., National Fire Academy) or demonstrate equivalent training and instructional prowess
Annual Refresher Training (q)(8)
- Competency must be refreshed or demonstrated every year.
- Employers are required to maintain documentation showing how this competency was assessed
Medical Surveillance (q)(9)
- HAZMAT team members and specialists must attend a mandatory baseline physical and ongoing medical monitoring under § (f)
- Any responder displaying symptoms after an incident must receive prompt medical consultation per (f)(3)(ii)
Be the first to comment