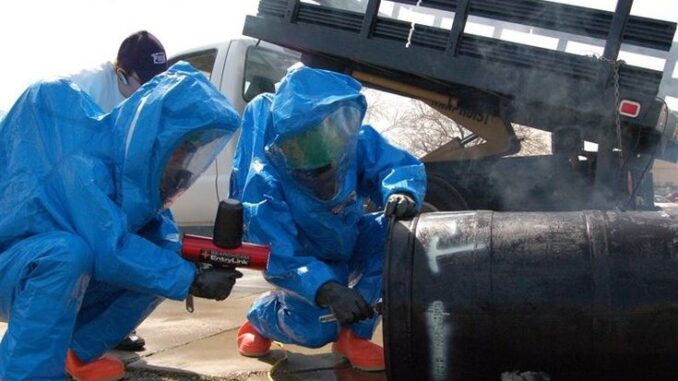
OSHA 1926.65a: HAZWOPER (continue….)
Medical Surveillance (1926.65(f))
Who Needs It? : OSHA 1926.65a: HAZWOPER
- Employees exposed to hazards for ≥30 days per year, including those wearing respirators or on HAZMAT teams.
- Who suffer from workplace exposure said by OSHA 1926.65a
When to Examine: OSHA 1926.65a: HAZWOPER
- At hiring, then annually (or biennially if approved by a physician).
- Upon job change or termination, if the last exam was over 6 months ago.
- Immediately after any signs of exposure, injury, or overexposure.
- For symptomatic or injured workers, as soon as possible after the incident, with follow‑up exams as needed.
What the Exam Covers: OSHA 1926.65a: HAZWOPER
- Reviews medical and work history, focusing on symptoms linked to hazardous exposures and ensuring the worker can safely wear PPE (like respirators) under site conditions.
- Specific tests are at the physician’s discretion, guided by OSHA 1926.65a: HAZWOPER manual.
Cost & Provider Credentials
- Exams are free to employees, during paid time, and conducted by a licensed physician—ideally trained in occupational health.
Doctor’s Report
- Employers must receive a written opinion, shared with the employee, summarizing:
- Medical fitness and PPE use
- Any recommended work restrictions
- Test results if requested
- Confirmation that the employee was informed of findings
- Confidential health details beyond this summary may not be shared.
Recordkeeping
- Employers must retain medical records per OSHA’s recordkeeping rules (29 CFR 1926.33), including test results, opinions, and exposure-related complaints.
OSHA 1926.65(g): Controls & PPE for Hazardous Worksites
Hierarchy First: Engineering & Work Practice Controls
- Use engineering controls and safer methods whenever possible to keep exposure below legal limits (e.g., sealed cabs, remote handling, isolating dusty operations, positioning workers upwind)
- If those aren’t feasible, combine controls and PPE to maintain safety levels
- Job rotation can only be used to reduce radiation exposure when no other control works
Applying Controls to Unregulated Hazards
- For hazards not governed by a specific OSHA limit, use engineering, work practices, and PPE to keep exposures below published safety limits (e.g., SDS or scientific studies)
Choosing the Right PPE
- PPE must be designed specifically for identified site hazards and work conditions
- Selection should consider PPE performance, site demands, task duration, and environmental factors
- Use positive-pressure respirators (SCBA or supplied-air with escape backup) if exposure poses immediate or serious health risks
- Wear fully-encapsulating Level A suits where skin contact could cause serious injury or impair escape Adjust protection levels (up or down) as more site info becomes available
- All PPE selections must comply with OSHA Subpart E standards
Monitoring & Suit Integrity
- Total-encapsulation suits must maintain positive pressure to seal out contaminants
- Air monitoring should guide PPE and control decisions to ensure exposures remain within safe limits, using instruments and site data
1926.65(g)(4): Fully Encapsulating Suits (Level A)
- Custom protection: These total-encapsulation suits must shield workers from the specific hazards identified on-site.
- Positive pressure: The suit must maintain internal air pressure to prevent contamination.
- Leak-tight performance: Compliance requires leakage of less than 0.5% during pressurized testing.
1926.65(g)(5): Written PPE Program
Employers must maintain a site-specific PPE plan covering:
- PPE selection and limits
- Duration of use
- Maintenance and storage
- Decontamination and disposal
- Fit, training, and safe don/doff procedures
- Inspection before, during, and after use
- Effectiveness reviews
- Consideration of temperature and heat stress
1926.65(h): Air Monitoring
- Purpose: Ensure exposures stay below permissible or published limits via air testing.
- Initial checks: First entry calls for tests for IDLH, oxygen deficiency, radiation, and flammable atmospheres.
- Periodic monitoring: Anytime site conditions change—new area work, container disturbance, unknown contaminants.
- High-risk sampling: Workers in heavy-exposure tasks (e.g., soil or container handling) must use personal sampling to track exposure levels
1926.65(i): Information Sharing
Provide all workers, contractors, and subcontractors with details about potential hazards, exposure levels, and protective measures before they enter the work area.
1926.65(j): Drum & Container Handling
- Safe practices: Transport and label hazardous materials per OSHA, DOT, and EPA guidelines.
- Pre-move checks: Inspect any drum or container before moving; if inaccessible (e.g., buried or stacked), relocate it safely first.
Handling Drums & Containers Safely (1926.65(j.1.iv–viii))
- Unlabeled containers are hazardous by default: Treat and handle them as if they contain dangerous substances until properly identified and labeled.
- Minimize movement: Plan site activities to limit how often containers are shifted.
- Warn employees: Inform personnel near containers before any movement operation begins.
- Prepare for spills: Keep DOT-approved salvage drums and absorbents nearby in high-risk areas.
- Major spill containment: Sites must have systems ready to isolate full volumes of spilled material.
Safe Container Transfer (1926.65(j)(1.ix–xii))
- Remove contents carefully: If a container can’t be moved safely, transfer material into secure functional vessels.
- Locate hidden containers: Use ground-penetrating or similar devices to detect buried drums before digging.
- Careful excavation: Dig slowly around buried containers to avoid accidental punctures.
- Fire protection: Match site fire suppression tools with OSHA Subpart F requirements.
Opening Drums (1926.65(j)(2))
- Air-line respirator care: Protect air connections and devices from contamination or damage.
- Restrict access: Only trained workers may open containers; others keep a safe distance behind shielding.
- Remote controls: Use explosion-resistant shielding for pre-opening controls and fire gear.
- Ignition control: For flammable atmospheres, only non-sparking tools and equipment may be used.
- Pressure relief: Safely vent container pressure, preferably remotely or shielded.
- No standing on drums
Specialized Containers (j.3–j.5)
- No ignition sources: Equipment used for handling must not create sparks or ignition risks.
- Radioactive contents: Assess hazards before moving or opening containers.
- Shock-sensitive materials:
- Evacuate unnecessary staff
- Use explosion-proof shields and barriers
- Maintain continuous low-impact communication
- Avoid moving bulging or pressurized drums until secured
- Handle laboratory waste (“lab packs”) as potentially explosive until characterized
Safe Handling of Shock-Sensitive Waste & Lab Packs
j(5) Shock-Sensitive Waste Controls
- Audible Alerts: Use alarm systems that are louder than ambient site noise and visible above surrounding light to signal start and end of explosive waste handling
- Ongoing Communication: Maintain reliable contact (radios, hand signals, phones) between the handler, site safety supervisor, and command post—avoid gear that could trigger reactions
- Pressurized Container Safety: Don’t move bulging or swollen drums until pressure causes are identified and secured
- Lab Pack Precaution: Treat containers with crystalline residue as potentially explosive until fully assessed
j(6) Handling Laboratory Waste Packs
- Expert Handling Only: Only trained personnel knowledgeable in waste classification should open lab packs
- Crystalline Alert: Any crystallized container must be treated as shock-sensitive until proven safe
j(7–8) Sampling & Transport
- Certified Sampling: Follow pre-approved, site-specific procedures when taking samples from drums/containers
- Safe Staging & Shipment:
- Identify and classify all drums/containers correctly before shipment
- Keep staging zones minimal, clearly marked, and with safe access routes
- Only combine wastes after complete characterization to avoid unexpected hazards
j(9) Tanks & Vaults
- Use Drum-Level Caution: Apply the same safe practices for drums and containers to tanks or vaults, scaled to their size.
- Follow Entry Protocols: Enter tanks/vaults only under approved, site-specific safety procedures
Be the first to comment